The Crucial Duty of Container Welding Examination in Ensuring Structural Honesty and Security Compliance in Industrial Applications
In the world of commercial applications, tank welding inspection arises as an essential aspect in protecting architectural stability and making certain conformity with security regulations. Making use of a combination of techniques such as aesthetic assessments and advanced screening methods, these examinations serve to recognize and reduce prospective flaws prior to they rise into significant threats. The effects of these methods expand past mere regulatory adherence; they essentially impact functional effectiveness and asset long life. Nonetheless, the intricacies bordering the examination process motivate a closer exam of its approaches and end results, revealing layers of relevance that benefit additional exploration.
Significance of Container Welding Examination
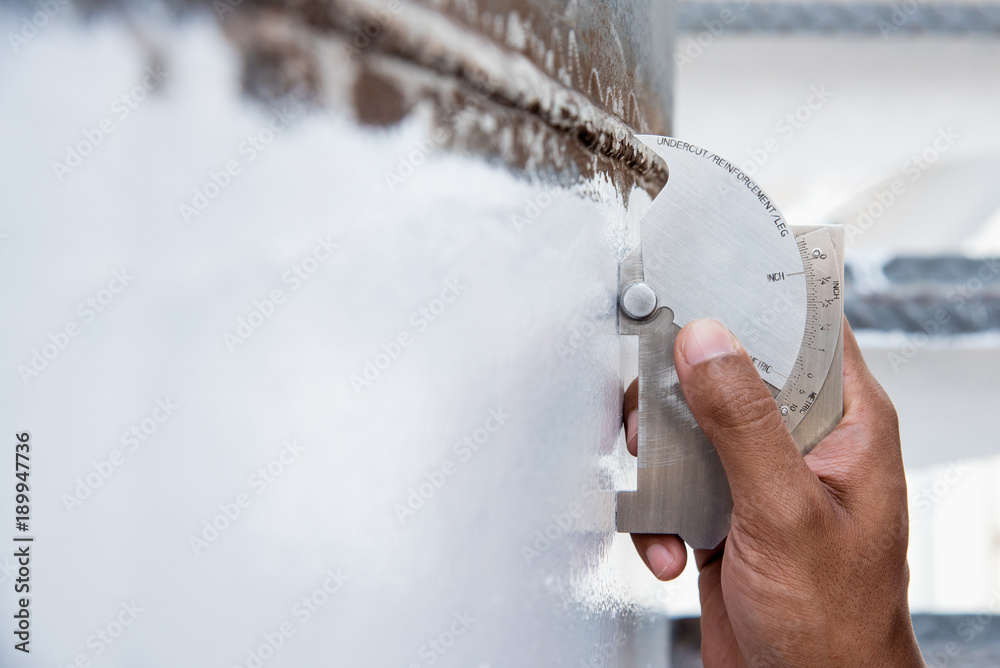
Making sure compliance with sector requirements and policies is one more considerable element of tank welding assessment. Governing bodies mandate rigorous guidelines for the building and upkeep of storage containers, and thorough evaluations aid organizations stick to these needs. Non-compliance can lead to extreme charges, including penalties and shutdowns, additionally stressing the demand for extensive evaluation methods.
In addition, storage tank welding inspection plays a vital role in preserving functional efficiency. In summary, the relevance of tank welding examination exists in its capability to guard public health and wellness, shield the environment, and guarantee conformity with regulatory structures.
Secret Inspection Techniques
Efficient storage tank welding examination counts on a variety of crucial methods that guarantee comprehensive examination of weld top quality and structural honesty. Among one of the most common techniques are visual examination, ultrasonic screening, radiographic testing, and magnetic fragment testing - Tank Welding Inspection. Each technique offers unique advantages in examining different elements of the weld
Visual assessment acts as the first line of defense, allowing assessors to determine surface area flaws, abnormalities, or inconsistencies in the weld bead. Ultrasonic testing uses high-frequency acoustic waves to spot internal problems, such as splits or voids, offering a comprehensive assessment of weld stability. This technique is especially effective in detecting issues that may not be visible on the surface.
Radiographic screening utilizes X-rays or gamma rays to produce photos of the welds, disclosing internal gaps and providing a long-term record for future referral. This technique is extremely efficient for vital applications where the danger of failing need to be minimized.
Last but not least, magnetic bit screening is employed to determine surface and near-surface defects in ferromagnetic materials. By applying electromagnetic fields and great iron particles, assessors can determine discontinuities that may compromise the architectural integrity of the tank. Together, these strategies form a durable framework for making sure high-grade welds in industrial applications.
Compliance With Safety And Security Requirements
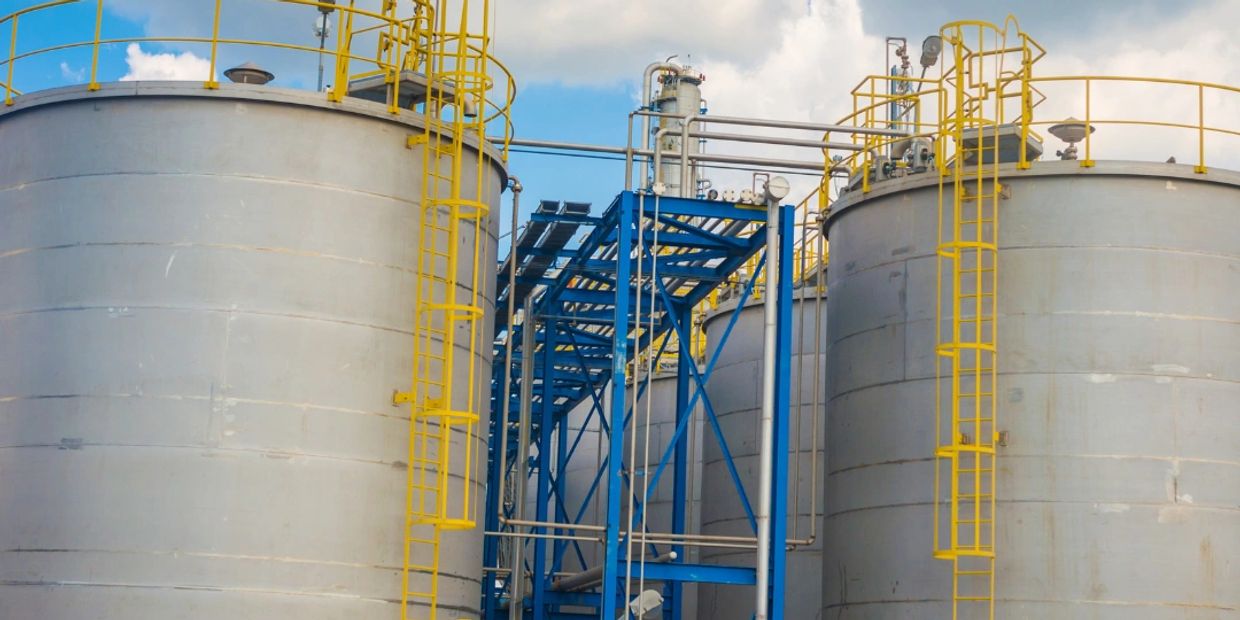
Regular evaluations play a crucial duty in making certain conformity by identifying potential failures or inconsistencies from recommended standards. Assessors are educated to review weld top quality, confirm product specs, and evaluate the overall architectural stability of storage tanks. Their proficiency is vital in ensuring that welding procedures fulfill the required safety and security criteria.
Additionally, conformity with safety criteria not only shields workers yet also safeguards the atmosphere from possible hazards such as leakages or devastating failures. Organizations that prioritize safety compliance are much better positioned to alleviate threats, enhance operational effectiveness, and cultivate a culture of security within their workforce. In recap, maintaining extensive compliance with safety and security requirements is crucial for the successful procedure of container welding tasks in industrial setups.
Advantages of Routine Inspections
Normal inspections are indispensable to preserving the structural stability and security of welded tanks. These examinations offer an organized method to identifying possible flaws or weak points in the welds, making certain that any type of concerns are addressed prior to they rise right into significant failures. By conducting routine evaluations, organizations can discover rust, tiredness, and other types of deterioration that may compromise container efficiency.
Additionally, regular evaluations contribute to conformity with industry laws and standards. Following these standards not just reduces lawful risks but likewise enhances the organization's track record for security and integrity. Routine inspections cultivate a proactive security society, urging staff members to acknowledge and focus on the relevance of equipment stability.
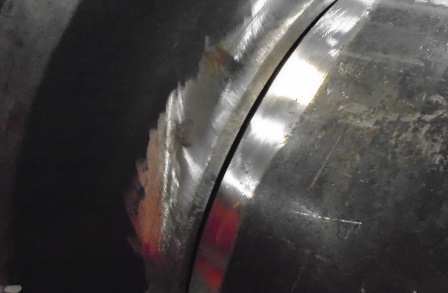
Instance Studies and Real-World Applications
Situation researches and real-world applications show the concrete impact of efficient container welding inspection methods. Adhering to the implementation of extensive welding inspection methods, including aesthetic and ultrasonic screening, the center determined important defects in weld seams that might have led to catastrophic failures.
Similarly, a water treatment plant applied a comprehensive evaluation program for its storage tank welding procedures - Tank Welding Inspection. By including non-destructive testing methods, the plant was able to identify very early indicators of corrosion and tiredness in weld joints. This timely treatment expanded the lifespan of the containers and made certain compliance with security guidelines, thus safeguarding public health
These instance research studies underscore the significance of regular and organized tank welding inspections. By focusing on these methods, industries can alleviate threats, boost architectural stability, and look at this website guarantee conformity with security requirements, inevitably resulting in improved operational performance and minimized liabilities.

Verdict
In final thought, container welding evaluation is a crucial component of preserving architectural stability and security in industrial applications. Using numerous assessment strategies ensures early detection of prospective problems, thus preventing tragic failings. Adherence to safety standards additionally improves functional reliability and conformity with governing needs. Eventually, routine assessments not only protect public health and wellness and the atmosphere but additionally add to the durability and performance of critical possessions, emphasizing the important duty of this technique in commercial operations.